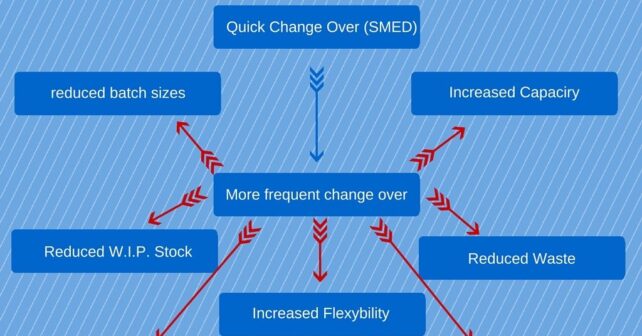
S.M.E.D.
Single minute exchange of die (cambio di un stampo in un minuto)
È un metodo ben noto per chi opera in ambienti lean manufacturing : lo studio continuo , preciso, quasi ossessivo spinto alla riduzione dei tempi di set up (attrezzaggio) di una macchina, attraverso la filosofia del miglioramento continuo.
I tempi di set up sono determinanti perché allungano molto il tempo di attraversamento dei pezzi nella linea di produzione senza aggiungere valore
Siamo quasi sempre concentrati a ridurre il tempo ciclo cercando macchine e utensili sempre più veloci e performanti con investimenti molto grandi quando, spesso, la soluzione più semplice, più economica e più efficace e quella di agire sui tempi di set up andando verso l’azzeramento dei tempi morti e dei fermi macchina.
L’idea dello Smed e il suo sviluppo è nata in Toyota ancora negli anni cinquanta e fu una precisa intuizione dell’ingegnere Shigeo Shingo che, per risolvere il collo di bottiglia determinato dal reparto presse, si rifiutò di comperare altre presse per aumentare la capacità produttiva ma, agendo sui sistemi di set up e il loro miglioramento, riuscì in poco tempo a ridurre del 50% il tempo di attraversamento, risolvendo il problema in modo molto più veloce e con investimenti molto inferiori. Ci sono esempi impressionanti di quello che si riesce a fare con lo SMED, famoso è un caso degli anni 70 sempre in Toyota dove c’era un collo di bottiglia su una pressa da 1000 tonnellate, il set up richiedeva 4 ore, spinti dalla concorrenza (Volkswagen) che per la stessa operazione impiegava 2 ore e mezza i giapponesi cominciarono a studiare il problema arrivando alla fine a compiere le operazioni di set up in soli 3 minuti.
La riduzione dei tempi di set up è estremamente importante perché oltre a ridurre i tempi di attraversamento rende possibile una maggiore flessibilità della linea. Se idealmente riuscissi ad azzerare tutti i set up potrei produrre un pezzo diverso dopo l’altro senza mai fermare le macchine o avere tempi aggiuntivi oltre al puro ciclo macchina. Soluzioni di questo tipo sono strategiche in un mondo come quello attuale, dove la richiesta del mercato è in cambiamento continuo ed è fondamentale, per soddisfare i clienti, essere in grado di produrre piccolissime serie in tempi rapidi, senza per questo aumentare i costi.
La riduzione dei tempi di set up attraverso il procedimento SMED permette di fare set up più frequenti con questi risultati:
- Riduzione della dimensione dei lotti
- Riduzione dei pezzi fermi lungo la linea ( WIP – wait in process Stock)
- Riduzione di tutti i magazzini
- Riduzione del lead time ( tempi di consegna)
- Aumento della flessibilità
- Aumento della capacità produttiva
- Riduzione degli scarti
- Aumento della qualità
Uno dei focus dello SMED è nel compiere più operazioni di set up possibili esternamente alla macchina (OED) in modo da ridurre al massimo il fermo macchina per le operazioni fatte internamente (IED)
Le attività a macchina ferma si definiscono IED (Inside Exchange of Die), mentre le attività che si possono effettuare mentre la macchina lavora si definiscono OED (Outside Exchange of Die). Ad esempio tutte le preparazioni, il trasporto delle maschere degli stampi e delle varie attrezzature possono essere effettuate mentre la macchina funziona. Il montaggio dei pezzi della macchina invece è un’attività che può essere effettuata soltanto quando la macchina è ferma. Se si riesce a organizzare in maniera ordinata le attività da svolgere nel setup e a suddividere correttamente le IED dalle OED si ottiene una riduzione del tempo di setup interno che va dal 30% al 50%
I passi dello SMED:
1) identificare il problema , darsi un obbiettivo
2) Descrivere, analizzare, quantificare le operazioni e determinare le attività non a valore
3) separare le attività che possono essere fatte esternamente alla macchina (OED)
4) Da IED a OED. identificare le attività fatte internamente alla macchina (IED) e quindi a macchina ferma che possono diventare esterne (OED) e cambiare in tal senso.
5) semplificare e standardizzare tutto
La nostra missione è rendere più semplice ogni processo, condividere esperienze e soluzioni, Le nostre attrezzature vengono immaginate, progettate e realizzate con il preciso scopo si semplificare i set up, ridurne i tempi e trasformare più operazioni possibili da IED a OED
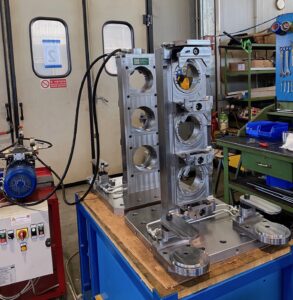
un esempio di una nostra realizzazione dopo un’analisi SMED: un cubo con fissaggi automatizzati per la lavorazione su quattro facce di una pressofusione senza bisogno di riposizionamenti,
I nostri ingegneri di processo sono a vostra disposizione per studiare tutte le possibilità
cliccate qui per richiedere una consulenza tecnica gratuita
MECSPE 2017