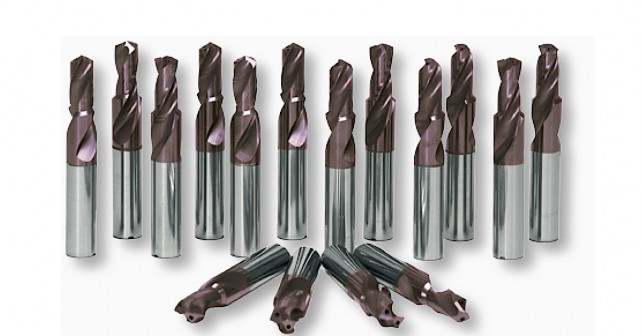
I rivestimenti superficiali per gli utensili da taglio:
Nella produzione di particolari metallici, utensili o altro, i processi di rivestimento sono una tecnologia antica. Da sempre si è capito che rivestire un metallo con diversi sistemi e con altri materiali consentiva di migliorarne l’efficacia mantenendo le fondamentali caratteristiche meccaniche.
In particolare nel mondo degli utensili si riescono ad ottenere delle durezze superficiali estremamente elevate senza aumentare la fragilità dell’utensili il che consente di avere velocità di taglio molto più alte, usura ridotta . maggiori caratteristiche antifrizione. Per tradurre in termini economici i rivestimenti consentono di aumentare molto la produttività diminuendo i costi per unità prodotta con un basso investimento iniziale (la sola differenza di prezzo fra l’utensile nudo e quello rivestito. La grande rivoluzione nel campo dei rivestimenti con la conseguente diffusione enorme degli utensili rivestiti è del 1987 quando la “Bloesch” , una società specializzata nel campo dei rivestimenti sottili, mise a punto un nuovo sistema ad arco catodico PVD.
PVD ( phisycal vapor deposition) ha permesso di superare i limiti delle vecchie tecnologie e ottenere rivestimenti in TiN (nitruro di titanio) e TiCN (nitro carburo di titanio) con spessori interessanti a temperature inferiori ai 500°, limitando moltissimo le tensioni interne al metallo dovute agli eccessivi riscaldamenti delle tecniche precedenti.
La tecnologia messa a punto dalla Bloesch su cui si è basata tutta la successiva industria del rivestimento ha come caratteristiche fondamentali:
– un’elevata stabilità dell’arco
– un costanza nel tempo dei ritmi di evaporazione
– un bassa formazione di goccioline (droplets)
– una formazione omogenea del plasma.
Nel sistema PVD attuale il meccanismo di deposizione avviene attraverso tre fasi: generazione, trasporto, deposizione. La generazione si ottiene per via fisica facendo evaporare i metalli che vanno a comporre il rivestimento. Il trasporto dalle sorgenti al particolare da rivestire avviene attraverso un plasma (gas ionizzato a bassa tensione). La deposizione sul particolare è agevolata dalla presenza di un campo elettrico.
Il metallo che comporrà il rivestimento ( ad esempio titanio o cromo o alluminio) viene evaporato per mezzo di un arco sottovuoto, la sorgente è a potenziale negativo (catodo) rispetto alla camera di deposizione ed è innescata con un corto circuito elettrico. Successivamente l’arco si muove sulla sorgente in maniera casuale o seguendo delle traiettorie pre definite dei campi magnetici. Durante il processo viene evaporata una quantità di metallo proporzionale all’intensità della corrente dell’arco. Il metallo vaporizzato altamente ionizzato viene accelerato nella direzione dei componenti da rivestire ( che sono polarizzati negativamente) e reagisce in parte con i gas reattivi introdotti nella camera ( -azoto- N2, carbonio- C2, idrogeno –H2) per formare il rivestimento duro.
I primi rivestimenti utilizzati alla fine degli anni 80 furono a base di Titanio nelle due tipologie più comune tuttora molto frequenti TiN (nitruro di titanio) da caratteristico colore giallo e TiCN (nitro carburo di titanio) dal caratteristico colore viola. In TiN presenta una maggiore capacità antifrizione , il TiCN una maggiore durezza superficiale.
A questi due rivestimenti se ne sono aggiunti poi moltissimi altri soprattutto multistrato in cui vengono combinati altri metalli e altri gas i più comuni oggi sono TiAlN ( nitruro di titanio alluminio), AlCrN (nitruro di cromo alluminio), AlTiNC (nitruro di titnio alluminio + carbonio amorfo), CrN (nitruro di cromo) , ZrN ( nitruro di Zirconio), Mos2 (solfuro di molibdeno).
Molte società produttrici di utensili hanno messo a punto rivestimenti multi strato particolari alternando le diverse composizioni per far avere le caratteristiche volute al tagliente dell’utensile.
Rivestimenti CVD ( chemical vapor deposition) è una differente tecnologia di rivestimento che viene utilizzata essenzialmente per utensili in metallo duro e per la deposizione di strati ceramici. Viene usata soprattutto per la deposizione di strati di CBN (nitruro di boro cubico ) o DLC ( diamante sintetico) .
Le caratteristiche dei due materiali sono estremamente elevate
– la durezza si avvicina a quella del diamante naturale (7000-12.000 HV) ( il CBN è meno duro e arriva ai 5000HV)
– il coefficiente d’attrito è molto basso simile a quello del teflon
– la reattività chimica è bassissima (in ambienti non ossidanti)
– la stabilità termica in atmosfera inerte è molto alta e supera i 1200 c°
– la conduttività termica è altissima
L’utilizzo di film di rivestimento in diamante sintetico piuttosto che l’impiego di utensili con il tagliente interamente in PKD (diamante policristallino) consente di avere le stesse caratteristiche di taglienza e resistenza all’usura con un costo molto più basso. La deposizione del film di diamante, però, può essere fatta solo su alcuni substrati perché la temperatura del processo è fra i 700 e i 1000 gradi quindi il substrato deve avere delle caratteristiche che lo rendano utilizzabile a queste temperature senza stravolgerne le caratteristiche meccaniche.
I rivestimenti con film CBN sono adatti per lavorare particolari in acciaio perché privi di carbonio – a elevate temperature di utilizzo il carbonio del diamante tende a legarsi con il carbonio presente nell’acciaio)
Anche per gli utensili rivestiti è necessaria la riaffilatura una volta che li tagliente perda le sue caratteristiche per la normale usura. Si può fare una semplice riaffilatura ma in questo caso la resa cambia moltissimo perché lo spigolo tagliente perde il rivestimento superficiale e la relativa durezza. E’ necessario quindi procedere , dopo la riaffilatura, ad un nuovo rivestimento. Le tecniche per togliere il vecchio rivestimento e rifarlo sono molto migliorate negli anni e si ottengono, oggi, degli ottimi risultati anche se , va detto, non si riusciranno più ad avere le stesse performance dell’utensile nuovo pur avvicinandosi molto.
La ricerca sui rivestimenti è continua e sempre più spinta, ogni giorno appaiono nuove soluzioni sempre più performanti e adeguate alle aspettative dell’industria moderna.
Nessuna Risposta to “Il rivestimento degli utensili, la strada migliore per ottenere grandi risultati.”