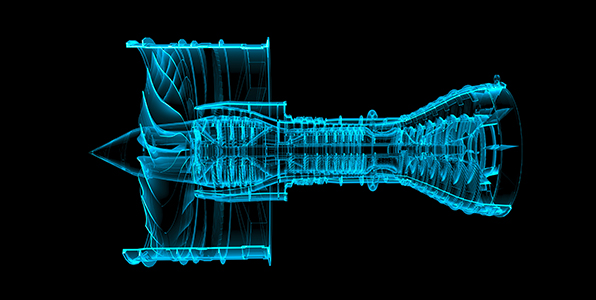
L’Italia è da sempre un paese all’avanguardia nell’industria aerospaziale. Fin dai primi del 900′ moltissimi costruttori hanno fatto la storia dell’aeronautica, da Caproni a Savoia-Marchetti, da Macchi a Fiat. Anche nella costruzione di elicotteri o di veicoli spaziali (vettori e/o satelliti) ci siamo sempre distinti. Le competenze ingegneristiche e manifatturiere in questo campo sono preziosissime e posizionano l’Italia fra i primi paesi al mondo. Una discutibile strategia politica ha tenuto fuori il nostro paese dal consorzio Airbus per non “dispiacere” il governo e le azienda USA, con cui da sempre c’è una grande collaborazione, che si sentivano minacciate dalla nascita di un consorzio Europeo. Nonostante ciò, moltissime nostre aziende sono fornitrici privilegiate di Airbus.
Alenia, ad esempio, costruisce in esclusiva la parte centrale delle fusoliere. Ma è sopratutto nei motori Rolls Royce, che equipaggiano la maggior parte degli Airbus, che la manifattura Italiana dà il meglio di se: in diverse aziende italiane vengono prodotti la maggior parte dei componenti fra cui le palette dalla turbina, tutte le strutture in titanio del motore e della turbina, tutti i tubi necessari per i vari circuiti. I motori Rolls Royce in uso su Airbus sono della tipo Trent, dei turboventola ad alto rapporto di diluizione che equipaggiano gli Airbus 330,340,350 e 380 e i Boeing 777 e 787, costituiscono il 40% dei motori aeronautici mondiali. Ad oggi Rolls Royce è il secondo costruttore mondiale di motori molto vicino al primo che è GE (general electric) .
Il particolare processo costruttivo delle pale – realizzate in Italia – (chiamato superplastic forming and diffusion bonding o SPF/DB) prevede la sovrapposizione esterna di due lamine di titanio su una struttura di rinforzo a nido d’ape (sempre in titanio) che si comporta come una travatura reticolare, il riscaldamento fino ad una temperatura che consenta la loro modellazione e saldatura seguita dall’insufflamento di un gas inerte (argon) che fa aderire i fogli esterni (che costituiranno il profilo della pala) allo stampo. Al centro del fan è collocata l’ogiva costruita in composito. Le pale possono ruotare a 3500 giri al minuto, con una velocità alle loro estremità di 1730 km/h, ben superiore a quella del suono.[8]
Su una versione 1000 in sviluppo è stata proposta una nuova tecnologia che impiega una costruzione ibrida fibra di carbonio/titanio (chiamata composite carbon/titanium o CTi) che promette di unire i vantaggi in termini di peso della fibra di carbonio con quelli della resistenza agli impatti con corpi estranei del titanio.[9]
Per darvi un’idea della potenza e delle dimensioni il Motore Rolls Trent XWB-97 del 2017 montato sui nuovi AIBUS 350-1000XWB ha una capacità di spinta di 144.351,9 kg/mt un peso approssimativo di 6300 kg, un diametro del fan di 3 metri e una lunghezza di 4,5 metri: un concentrato di potenza, tecnologia e affidabilità assoluta.
Molte volte tendiamo a sminuirci e a considerarci un paese con una tecnologia limitata, niente di meno vero: siamo un grandissimo paese con un industria tecnologica ai massimi livelli mondiali proprio dove serve affidabilità, qualità, sicurezza ed ingegneria evoluta. I nostri tecnici, i nostri ingegneri, le nostre aziende si distinguono nel mondo per capacità elevatissime. Dovremmo essere orgogliosi per ciò che facciamo e sappiamo fare e ricordarlo sempre: l’Italia è un grande paese.
MECSPE 2017