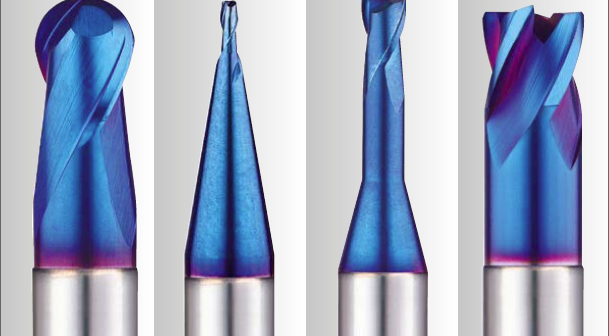
La maggior parte degli oggetti con cui entriamo in contatto nella vita di tutti i giorni, dall’auto che guidiamo alla penna che usiamo per scrivere, sono stati realizzati a partire da uno stampo. Senza contare poi le machine produttrici di qualsiasi tipo.
Va da sè che quello degli stampi sia un mondo ampio, vario e tra i più complessi della meccanica. Gli stampi, infatti, possono essere diversi per dimensione, per materiale di partenza e per i trattamenti termici a cui sono sottoposti. E se è scontato che migliore è lo stampo, migliore è la qualità dell’oggetto che da esso viene prodotto, lo è altrettanto immaginare che gli stampi, data la grande varietà, non abbiano tutti le stesse esigenze di lavorazione.
In mezzo alla molteplicità di tipologie e all’eterogeneità delle situazioni, riscontriamo tuttavia un elemento comune: il 90% degli stampi è costruito per fresatura, mentre solo per precisioni elevatissime, nell’ordine di pochi centesimi di millimetro, si usano processi come l’elettroerosione o la fotoincisione.
La fresatura consiste nell’asportare dei pezzi di materiale attraverso uno strumento, la fresa, in modo da tagliare e sagomare il pezzo secondo la forma prestabilita. Con la fresatura è possibile realizzare superfici piane, con scanalature, semplici o complesse.
L’operazione di fresatura prevede una fase di sgrossatura, in cui si ha una prima rapida asportazione del materiale, una fase di semifinitura e una di finitura. Alla fine il progetto deve essere rispettato sia per quanto riguarda le tolleranze delle dimensioni sia per il grado di rugosità delle superfici.
“La gamma di frese oggi disponibile per compiere al meglio queste operazioni è grandissima – spiegano dall’Ufficio tecnico di YG-1, azienda leader nella produzione di utensili da taglio -. Ci sono frese ad elevato avanzamento ideali per la fase di sgrossatura, frese toriche o semisferiche, frese per acciai durissimi ma anche basso legati, frese con un diametro che può variare da un decimo fino a 25 mm, frese in grado di riprodurre tutte le geometrie possibili e quindi adatte per qualsiasi applicazione”.
Quali sono le problematiche nella costruzione degli stampi? E quali le innovazioni nella tecnica di fresatura che possano aiutare a risolverle?
“Oggi è importante soffermarsi, oltre che sulle diverse tipologie di frese e sulla scelta di quella più adatta per ogni operazione, anche e soprattutto sulle tecnologie che permettono di utilizzare al meglio gli utensili. Affinché lo stampista riesca a garantire la massima precisione nella fase di finitura entrano in gioco le tollerenze degli utensili, la qualità dei materiali di base, il loro rivestimento e il bloccaggio.
Nel caso di lavorazioni senza presidio è necessario assicurarsi che la fresa lavori per tutto lo stampo senza usurarsi, perché se il diametro della fresa cambia, quei centesimi si ritrovano poi nello stampo ed è necessario sottopporlo ad un’ulteriore lavorazione. Spesso, inoltre, capita che lo stampo sia costituito da una figura complessa e che gli utensili standard non consentano di raggiungere tutte le parti da lavorare”.
Come procedere in questo caso?
“Oltre ad utensili e attrezzature speciali, è possibile sfruttare le potenzialità dei centri di lavoro a 5 assi, perché gli assi rotativi supplementari consentono un accesso facilitato ai profili complessi del pezzo, come le cavità; un valido aiuto viene anche dalle tecnologie informatiche: il sistema Cad per progettare e visualizzare il prodotto, e il sistema Cam per programmare e guidare le operazioni delle macchine robotizzate che realizzano il prodotto stesso. Infine, non bisogna dimenticare l’importanza dei sistemi di bloccaggio. Nel caso di figure complesse si può ricorrere a mandrineria modulare o a mandrini a calettamento termico che, oltre a garantire la massima precisione, sono lunghi e sottili dato che non presentano ingombri per il fissaggio”.
Da sinistra: il disegno tecnico, il disegno CAM e il particolare finito
In cosa consiste il calettamento termico?
“È una tecnica che sfrutta la naturale tendenza del metallo a dilatarsi e restringersi in base al calore al quale è sottoposto. Il mandrino viene scaldato fino a raggiungere la temperatura adatta a espandersi per accogliere il gambo dell’utensile scelto. Il successivo raffreddamento, che restringe il mandrino intorno alla fresa, permette un serraggio precisissimo, ad alta tenuta, ideale per lavorazioni dove gli spazi di manovra sono ridotti e le profondità risulterebbero critiche per i sistemi tradizionali”.
MECSPE 2017