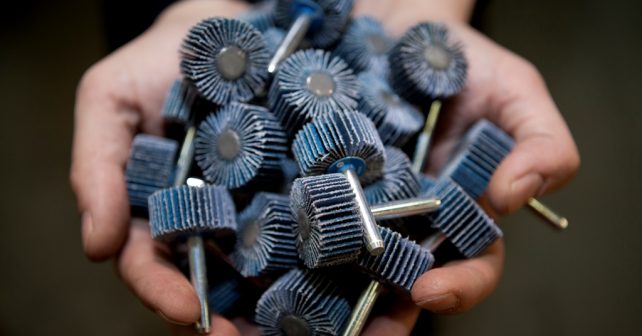
Le ruote lamellari sono prodotti utilizzati nella lavorazione meccanica per operazioni di smerigliatura, sgrossatura e finitura di acciai inossidabili, metalli non ferrosi e altri materiali, anche in zone difficilmente accessibili. A ogni operazione corrisponde una ruota adatta: ad esempio per la smerigliatura e sbavatura si utilizzano ruote in tela, per operazioni di finitura è più adatto il panno abrasivo. Le ruote lamellari possono essere allestite su gambo o con flangia a seconda delle esigenze d’impiego. La fattibilità prevede misure comprese tra 10mm e 80mm di diametro per le ruote su gambo e da 80mm a 400mm per le ruote con flangia.
Apparentemente sempre le stesse da quando hanno fatto la loro comparsa negli anni 40, le ruote lamellari hanno invece subito un’importante evoluzione.
“C’è una continua ricerca sia di nuovi materiali che di nuovi metodi per creare prodotti in grado di garantire una sempre maggior efficienza ai clienti: prodotti più durevoli, materiali più performanti, metodologie di lavoro più avanzate e processi produttivi sempre aggiornati – spiega Andrea Boselli, responsabile vendite di zona di Cta Calflex, azienda specializzata nella trasformazione di abrasivi flessibili per l’industria-. Ci affidiamo a partner d’eccellenza e controlliamo la produzione passo per passo nello stabilimento di Albairate. Per noi la materia prima e il processo produttivo completamente Made in Italy sono fondamentali”.
Quali sono le novità dal punto di vista dei materiali?
Le ruote lamellari seguono l’evoluzione della materia prima, cioè dell’abrasivo: corindone, zirconio, carburo di silicio, abrasivo ceramico e abrasivo a grani microreplicati. Quest’ultimo è l’applicazione più recente e consente di avere un consumo estremamente omogeneo e una rifinitura molto costante.
Per quanto riguarda invece le metodologie realizzative?
Una ruota lamellare per essere ottimale deve rispondere fondamentalmente a due requisiti: deve consumarsi “fino all’osso” ed essere perfettamente bilanciata. Il primo è un requisito importante in termini di risparmio; il secondo, invece, significa mettere l’operatore in condizione di lavorare a lungo al meglio, senza il disagio provocato da eventuali vibrazioni. Sono obiettivi che otteniamo grazie all’evoluzione tecnologica dei macchinari con cui vengono realizzate le ruote lamellari, macchine mai standardizzate ma personalizzate appositamente dal nostro dipartimento di ricerca e sviluppo”.
Come individuare il prodotto più adatto alle proprie esigenze all’interno della vasta gamma di prodotti a disposizione?
Non c’è una regola fissa e attingere alle conoscenze, ai consigli e al bagaglio di esperienza di un tecnico specializzato in abrasivi è fondamentale, soprattutto per le richieste più particolari.
Quali sono i consigli di utilizzo per ottimizzare le operazioni e quindi la produttività?
Il primo consiglio che può sembrare banale è scegliere prodotti di qualità che permettono di operare in modo efficiente e soprattutto di ridurre i fermi di lavorazione.
Bisogna inoltre prestare attenzione a utilizzare gli utensili secondo le indicazioni tecniche fornite: il numero dei giri, ad esempio, deve essere quello indicato. Bisogna anche scegliere accuratamente l’abrasivo e la grana più adatta alla propria necessità applicativa. Ad esempio il corindone per l’approccio generico sui metalli, il carburo di silicio per i metalli non ferrosi, lo zirconio per l’acciaio inossidabile, l’abrasivo ceramico per impieghi gravosi con metalli che rischiano di surriscaldarsi. L’abrasivo a grani microreplicati, invece, è ideale per l’acciaio inossidabile quando sia richiesto di abbassare al massimo la rugosità delle superficie, ad esempio nel settore alimentare o chimico-sanitario, dove le esigenze igieniche hanno standard particolarmente elevati.
Per ultimo suggeriamo sempre di montare l’utensile su macchine di affidabilità comprovata.
MECSPE 2017